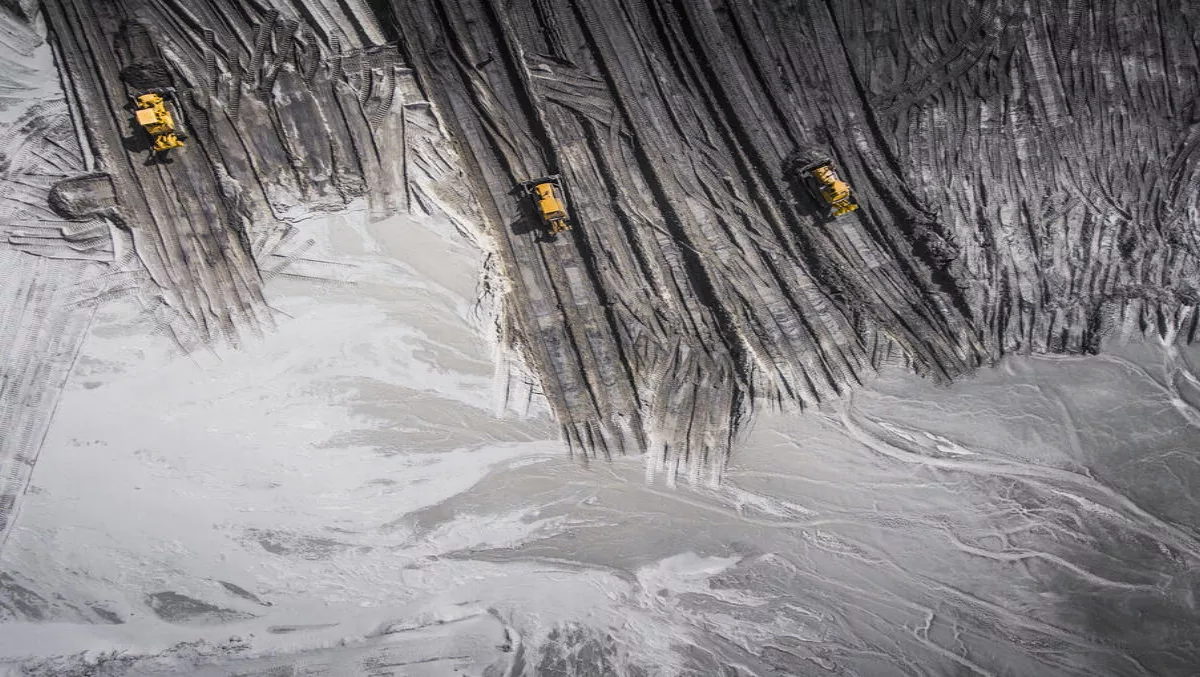
Like other industries, recently mining has been going through a technological shake up.
In addition to improvements in automation and safety, sophisticated new IT solutions are boosting productivity and competitiveness whilst reducing operational costs.
Case in point, Fortescue Metals Group - one such mining organisation that has reported enormous gains, including 10 and 20% increases in productivity alongside $30 million in annual cost savings, thanks to its deployment of advanced technologies across a number of mining sites.
Fortescue Metals Group has reported its use of real-time reporting of productivity data to mobile devices of its field operations team, and its use of autonomous haul trucks are at the heart of these rewards.
With the adoption of advanced and connected equipment, including driverless mining trucks, on-board and off-board computer systems and remote operations centres, the need to monitor assets and networks has brought with it a new set of requirements for the IT infrastructure of mining organisations.
For example, with a huge focus on boosting productivity within mining, there is significant pressure on ensuring that technology remains operating 24/7.
High levels of redundancy are expensive and will not be an option for numerous remote mining sites, which makes proactive detection of imminent failures paramount.
With this in mind, the need to monitor assets, and the networks connecting them, is critical to mining today.
But with the potential for so many “connected” machines and processes on a mining site at any given time, knowing where to start is often the first hurdle to successful network monitoring, both in mining and beyond.
The role of remote power
The first area of consideration is the foundation of any operations - that is remote power.
With the wireless network, delivering power to a number of access points across a large mine can only be achieved with remote power, such as solar, generators and wind.
These solar solutions are engineered specifically for particular mines as precise calculations are required to place solar panels successfully across a site, to meet energy demands.
Despite the mathematics involved, due to maintenance issues and other environmental factors, a number of these solar deployments have gone offline due to depleted batteries and lack of generated power from the solar panels.
However, many mining companies have seen the light and recognised the potential of connecting their power sources to their networks and allowing network monitoring to do the watching for them.
For example, if a battery begins to deplete more than expected, or if the voltage is incorrect, employees across a mine can be notified and can proactively resolve issues with power before they occur.
Mining equipment monitoring
With the introduction of autonomous and semi-autonomous mining trucks comes the emergence of a huge number devices on a mining site's network.
These machines (or devices) are constantly feeding data back to the operation and maintenance teams, whether they are fully autonomous vehicles or not.
This has increased the perimeters of a mine's network immensely and results in huge volumes of data being sent across sites, and to alternative locations, from across machines.
Interfacing these systems, to collect and fully leverage the data coming from a mine, requires a huge amount of customisation – from database sensors and custom scripting, to the deployment of gateways to successfully convert data.
That said, for those who make such changes, the rewards will be worth it - the potential applications for this type of monitoring on a mine include vehicle position, load data and vehicle health - critical to increasing productivity hugely.
For example, if any sensors are unresponsive on a machine, vehicle operators are alerted and can respond accordingly - hopefully able to fix problems as they arise, to keep machines running.
Mine site environmental monitoring
Most mines can be environmentally challenging to work in.
Dust, moisture, water run-off, as well as outdoor exposure to sunlight, wind and rain.
This can undoubtedly have an impact on the equipment, operators and the community living nearby.
Government bodies in Australia such as the New South Wales Environmental Protection Agency (EPA) have been tasked to monitor and minimise the environmental impact from the neighbouring coal mines, which directly impacts the coal mines and the environmental levels that they have to adhere to.
Mining companies have a responsibility to minimise the impact of their operations within the local environment, it is therefore vital that they are able to easily measure environmental metrics such as air and water quality, noise levels, ground stability, wind speed and direction and humidity.
For example, weather stations have quickly become another go-to connected device used by mining organisations to monitor environments and pull data from sites regardless or whether they are stationed and with no disruption to the workforce.
As we've seen with remote power and equipment monitoring, environmental data can be fed back to teams across a mining project or organisation, in a timely manner, to keep people and machines safe and operations running smoothly.
As the mining industry becomes more connected, tools to monitor physical sites, people and machines will become critical to everyday operations.
With the ability to provide visibility into mining operations, network monitoring holds the key to tremendous gains including increasing productivity and bonus cost savings.
In addition, network monitoring allows mining to dig a little deeper - providing the visibility into the technology infrastructure to ensure issues are detected before they become critical disruptions.